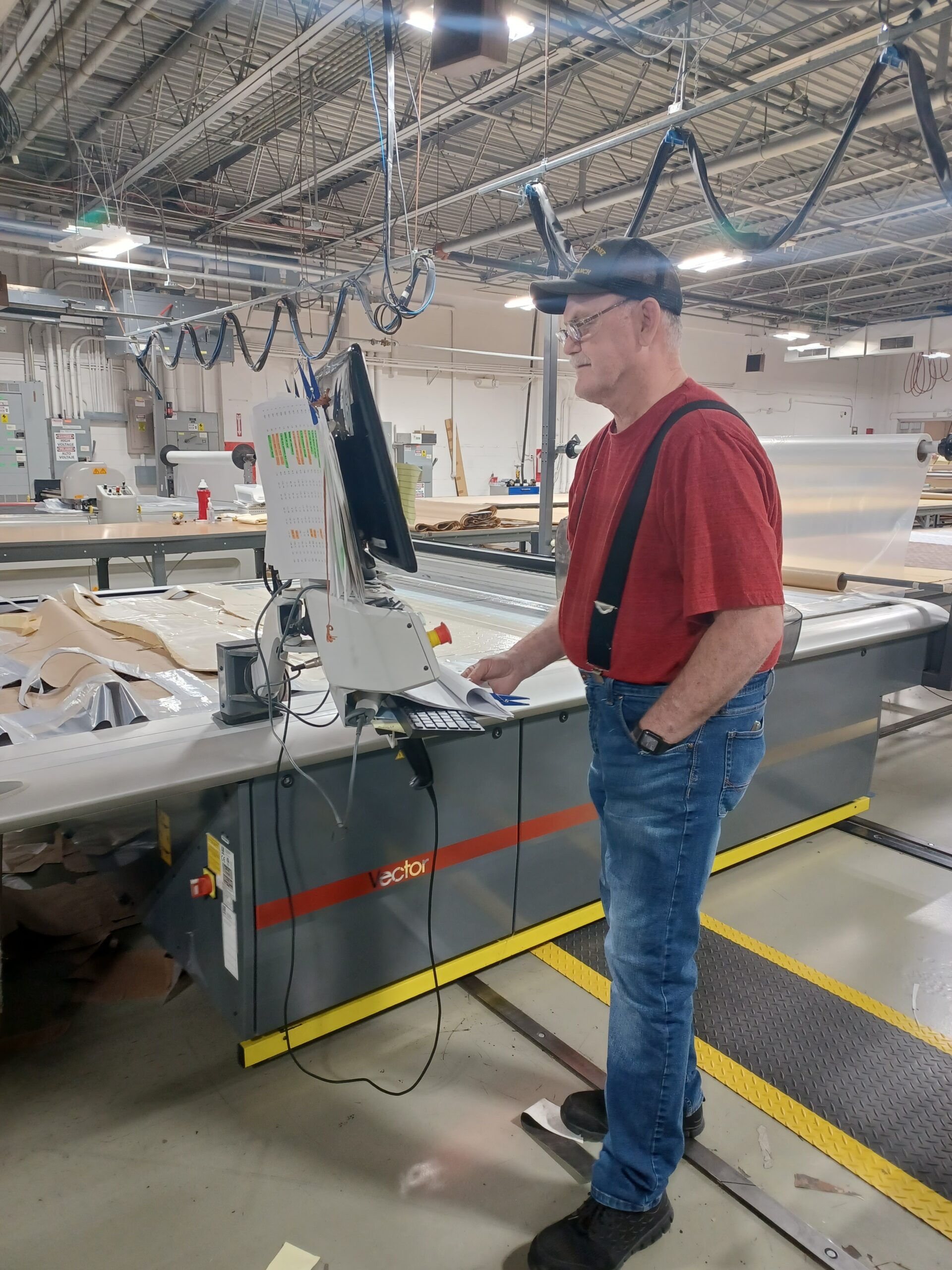
Keeping Firefighters Safe: MSA Safety and Innovations in Manufacturing
March 22, 2023 by Jessika Leatherbury
By: Sunnie Dawn Baker
A willingness to change lies at the heart of innovation. Many times, these changes come out of necessity. In the case of MSA Safety, a local manufacturer that produces Globe firefighter gear, these innovations lead to increased productivity and products. Many people in our region are unaware of Globe as a manufacturer which produces firefighting gear that is sent all over the country, as well as to Canada and Puerto Rico. The work that they do puts innovation to work so their products can save the lives of firefighters, which in turn helps them do the work of saving the lives of others.
Globe Manufacturing is a part of MSA Safety, and they create high quality coats, pants and other protective clothing for firefighters. This work is highly regulated in the United States because the business of fighting fires is so incredibly dangerous. Their products are regularly tested by Universal Laboratories (UL) in order to make sure that everything is up to the proper standards. For instance, they have to make sure that everything is completely water tight, where no stray holes could let steam or other harmful chemicals in the suit. However, considering that all of these garments are sewed together, that is no small feat. A single stray needle hole could be disastrous for a firefighter so the production of these garments needs to be very carefully done while also producing a high quantity of suits in order to keep up with demand.
Shane Hudson, the plant manager at MSA Safety in Ada, Oklahoma, actually came to this position from the world of oil and gas and heavy manufacturing. While his wife loves to sew and his grandmother sewed, he had some, though little, experience in the field. However, he had expertise in a manufacturing philosophy called “Lean Manufacturing.”
This way of thinking comes from an American engineer, W. Edwards Deming, who was trying to find ways to make manufacturing more efficient by eliminating different types of wastes: motion, waiting, conveyance, correction, inventory, overproduction, and overprocessing. In essence, he was trying to overhaul the entire experience of manufacturing so that the workers and companies could more effectively use their time, energy, and resources. When he first approached American manufacturers with his prospective overhaul of their processes, he was rebuffed. However, when he approached Kiichiro Toyoda, who founded the Toyota Motor Corporation, his ideas were accepted. This philosophy of lean manufacturing helped rebuild the post-war economy of Japan and eventually these ideas were accepted in America as well.
Hudson is passionate about the ideas in lean manufacturing and applies them to the local MSA plant. The status quo isn’t enough for him; he is constantly evaluating their processes and procedures to see how everything can be more productive and waste less time, energy, and resources. Sometimes these improvements come in the form of new and better equipment, but also sometimes it can come in adjusting the flow of work from one employee to another. Due to these advances, in the past two and a half years that Hudson has been at the plant, production has more than doubled; they produce around 160 firefighter suits a day. This increase in production has also led to more jobs in the community. When he started, they had 50 employees; now they have 120.
In addition to streamlining the manufacturing processes, the plant also employs many technological innovations that help with this as well, including automation. This automation makes the product more consistent while also eliminating wasted time and materials. However, this streamlining does not eliminate jobs, but rather encourages more technical jobs because workers still have to know how to use the computers and monitor the work. They have modified embroidery machines that attach the Velcro to the garments, using the same stitches every time as well as lettering machines that stitch the names on the garments, using a pattern supplied on a computer file. One of their most interesting machines is a cutter that cuts 18 layers of material at once. The material is held in place by a vacuum while the machine fits the most pattern parts it can out of the material, eliminating as much waste as possible.
These computer functions are done using a bar code that is unique to each suit. A bar code accompanies the order from station to station, and this is one of the most innovative, and necessary, aspects of this process. As per the American regulations, every firefighter suit is required to be individualized for each person and measured to fit. This is not the type of manufacturing where they produce 160 identical items every day. Every pair of pants and every coat is going to be unique. This goes beyond the basic measurements, but also the types of materials, styles and locations of pockets, different types of straps, various types of trim, as well as many other different options. Hudson says, “Everything is incredibly customized. There are millions of different options and combinations to choose from.” For reference, there are 25 different materials that could be used on the outside as well as multiple options for both layers on the inside. The list of possibilities for pockets and trim goes on and on, and this is why the bar code is so important. From the very beginning the code tells workers which materials to load onto the cutting table, but then it will also tell the cutter how to most effectively cut the materials. Then this bar code will travel along to every station, telling the worker what they need to be doing so they don’t have to dig through all of the different options, eliminating both a waste of time and energy for the worker but also making mistakes less common.
The world of manufacturing necessitates different types of innovation, whether it is reconsidering the flow of work from one individual to another or employing new types of technology for efficiency and accuracy. MSA Safety embodies both of these types of innovations while dealing with a product where they cannot be any mistakes. It is one thing if a shirt you buy off the rack has an imperfection. It might be annoying, but there are no serious consequences. For the suits they make at MSA Safety, however, a single imperfection could literally mean life or death for both the wearer of the suit and the person they are trying to save. Hudson is proud of the work they do at his plant and continually impressed with his workers’ talent and dedication to perfection. While they might not be fighting the fires themselves, they are making it possible for it to be done safer.
Sign up to receive more news from the Ada Jobs Foundation HERE!
Written by
Jessika Leatherbury
You may also interested in:
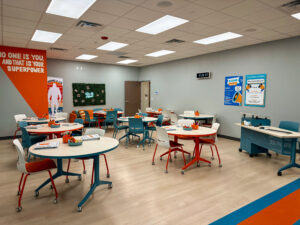
BUILDING FUTURES: WORK READY ADA CELEBRATES ITS FIRST YEAR
BY: CATHLENA SPENCER Just one year ago, Work Ready Ada, a new employment readiness program, was launched in partnership with Pontotoc Technology Center (PTC). The program, funded by Oklahoma Human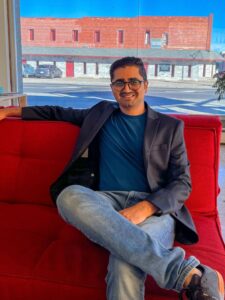
AI IN EDUCATION: A CONVERSATION WITH VINAYAK MITTY
BY: SUNNIE DAWN BAKER One of the areas in technology with the most potential for entrepreneurial growth is Artificial Intelligence (AI). AI is increasingly shaping every part of our lives,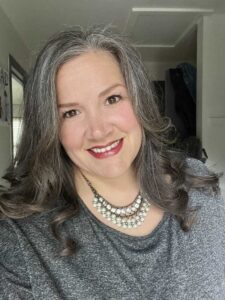
Adapt and Overcome: Allison Poe’s Recipe for Resilience and Growth
By: Sunnie Dawn Baker Allison Poe has always followed her feet. She waits for the signs to appear and, once she recognizes them, she travels that path, and has never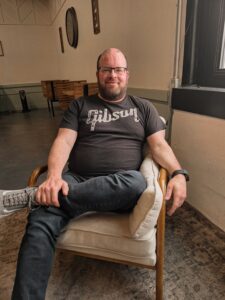
Jeff Warren: A Life in Sound, Vision, and Storytelling
By: Sunnie Dawn Baker When Jeff Warren got involved in the Houston music scene as a teenager, he had no clue where his path would lead. Now, nearly thirty years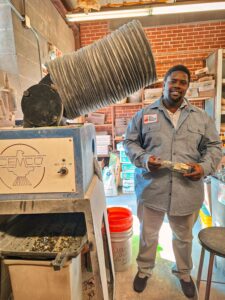
From Pitch to Progress: ECU's Glass Recycling Program Turns Waste into Opportunity
By: Sunnie Dawn Baker In 2018, Dr. Christine Pappas competed in Ada Jobs Foundation’s Big Pitch Competition by promoting grinding glass bottles into sand. She won the Big Pitch that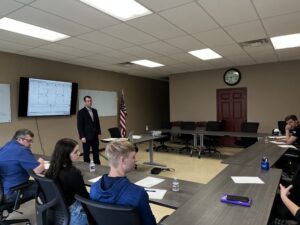
The Importance of Customer Discovery: Know Your Audience and Know Your Market
By: Sunnie Dawn Baker Entrepreneurs and small business owners must consider many factors to achieve success, with their target market being one of the most crucial. Sometimes, when people are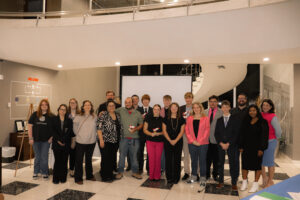
What Does Economic Development Do for You? The Significance of the Economic Multiplier
By: Sunnie Dawn Baker People often find the term “economic development” vague and confusing. Understanding how economic development works and benefits the community can be challenging. Though there are many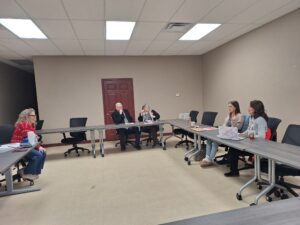
Helping Entrepreneurs One Workshop at a Time: Lauri Rowe and QuickBooks for Small Businesses
Entrepreneurs tend to be filled with passion and big ideas. They have found a solution to a problem they see in the world, and they barrel ahead, excited for their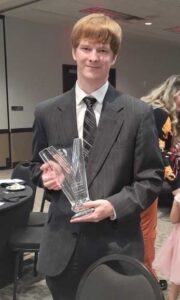
Hunter Cook: Technology, Entrepreneurship, and the Written Word
By: Sunnie Dawn Baker Hunter Cook started writing when he was seven years old. At first, he wanted to write comic books, but then he realized he couldn’t draw. He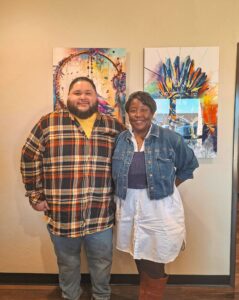