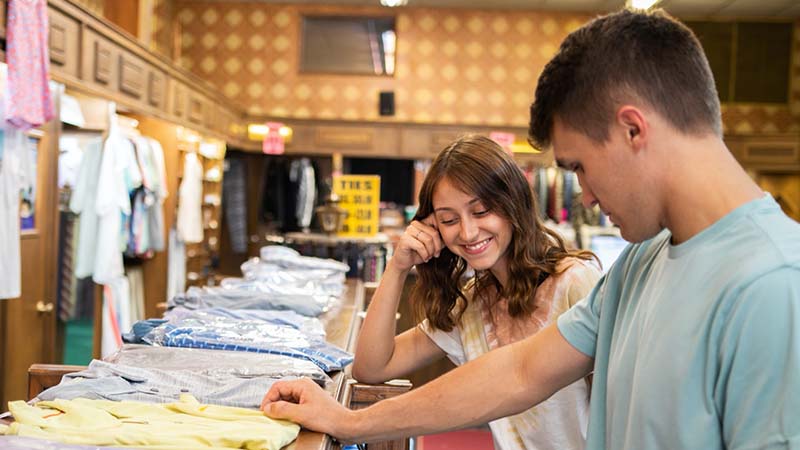
Jannette Orr stood on MSA’s Globe turnout gear manufacturing floor in Ada and held up a firefighter coat that was under construction at the plant.
Bright yellow letters on the back read “OKLA CITY.”
Globe’s Ada plant and its 48 employees are producing 510 sets of three-layer firefighter jackets and pants for the Oklahoma City Fire Department, said Roger Page, operations manager for Globe’s three production facilities in Ada, Pittsfield, New Hampshire, and Auburn, Maine.
“Recently, we reacquired the Oklahoma City contract,” Page said as he led me and colleagues from the Oklahoma Center for the Advancement of Science and Technology (OCAST) on a tour of the Ada production plant.
“Oklahoma City had previously been in our gear, and we’re excited to have them back,” he said.
Globe was founded in 1887 as a family-owned producer of protective clothing for firefighters and headquartered in Pittsfield, New Hampshire. It was acquired in July 2017 by MSA Safety Inc., a publicly traded corporation based in Pittsburgh.
Globe opened the Ada plant almost 16 years ago.
“We were having a really hard time hiring enough workers in the Pittsfield area, and we learned that Wrangler was leaving this area and had a very similar weight of fabric to that which we use,” said Page, who has worked for Globe for 36 years. “We decided to explore this area, and the Ada Jobs Foundation did a great job, almost recruiting us.”
Coalgate native Orr was among the former Wrangler employees who migrated to Globe, starting on the production floor as a stitcher. Today she is the plant manager, and personally trains new hires on the complexities of running sophisticated machinery.
“Our workforce here is doing great,” Orr said. “We try to start them off on the right track. They work hard and steady. We make sure they have good benefits, because the employees here are like family.”
Globe uses what is known as the Toyota Sewing System in Ada to assemble the firefighter suits. It’s a manufacturing philosophy that began in Japan and moves each garment from station to station.
“As you look around the facility here, everything is done in single piece flow, with standup operations and more machines than there are people because they bump their operations as they go through the cell,” Page said. “It makes the operations a lot more flexible, and the workers aren’t stuck in one spot doing the same thing all day.”
Globe produces two of its seven styles of “turnout gear” or “bunker gear” — insider speak for firefighter protective apparel — at the Ada plant. Each firefighter garment has three layers that consist of an outer shell, a thermal liner and a moisture barrier.
“We have a host of options that can go on those base garments,” Page said. “For example, we have over 400 different sizes of radio pockets alone.”
Globe’s operation has benefited from a relationship with the Oklahoma Manufacturing Alliance, which is a partner with OCAST in the Oklahoma Innovation Model that provides assistance to small manufacturers and new ventures across the state.
“I’m just really impressed with the amount of effort that Oklahoma puts into supporting manufacturers, whether it’s the Ada Jobs Foundation, the Pontotoc Technology Center training center or the Oklahoma Manufacturing Alliance,” Page said. “All of that is phenomenal.”
In addition to Oklahoma City, Globe produces garments for firefighters in numerous other Oklahoma communities. Ada’s proximity to Oklahoma City afforded the city’s fire department an opportunity to eyeball the equipment under construction, Page said.
“It’s only fitting to be able to produce Oklahoma City’s firefighting gear an hour and a half away here in Ada,” he said. “They are excited to come down and watch their gear being built and meet the people building it.”
Jim Stafford writes about Oklahoma innovation and research and development topics on behalf of the Oklahoma Center for the Advancement of Science & Technology (OCAST).
Written by
kylernixon
You may also interested in:
From Foundation to Growth: Ada Jobs Becomes Grow Ada
By: Sunnie Dawn Baker For 27 years, the Ada Jobs Foundation, in partnership with the City of Ada, has led the economic development efforts in the community. Funded by the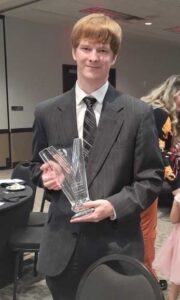
Hunter Cook: Technology, Entrepreneurship, and the Written Word
By: Sunnie Dawn Baker Hunter Cook started writing when he was seven years old. At first, he wanted to write comic books, but then he realized he couldn’t draw. He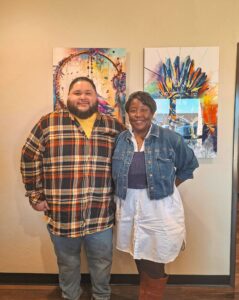
Empowering Native Artists: FAME App Brings Innovation to First American E-Commerce
By: Sunnie Dawn Baker Entrepreneurs are problem solvers. They are constantly striving for solutions to issues they see in the world or in their own lives. In the case of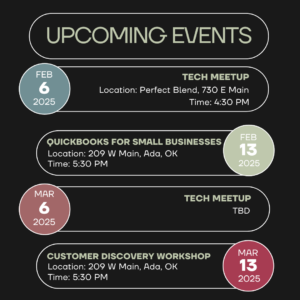
Learn, Connect, and Grow: 2025 Workshops for Aspiring and Current Business Owners
By: Sunnie Dawn Baker A new year brings new possibilities, and, at the Ada Jobs Foundation, it also brings a new round of programming and workshops. As the local Economic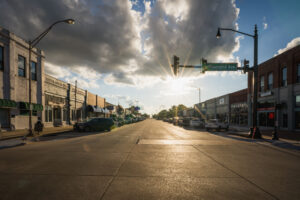
Making a BIG Impact in a Small Town: Over a Million Dollars Invested with the Business Improvement Grant
By: Sunnie Dawn Baker All over Oklahoma, and the country, downtowns are disappearing. It is not uncommon to travel through a small town and see once bustling Main Streets abandoned—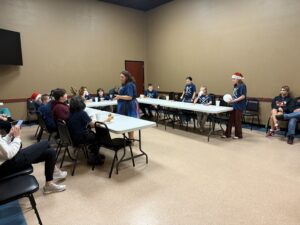
Conduit Coders Make History: National Champions in Youth Coding League
By: Sunnie Dawn Baker Friday, December 13th , marked the end of another season for the Conduit Coders, the Youth Coding League team that the Ada Jobs Foundation supports with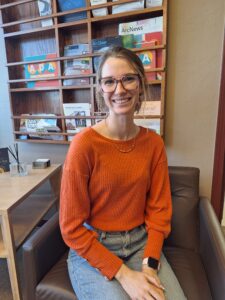
Grind and Shine: Kaibree Flood’s Journey from Student to Entrepreneurial Storyteller
By: Sunnie Dawn Baker Sometimes it is the unexpected moments in life that can lead to new and surprising journeys. In the case of Kaibree Flood, the unexpected was a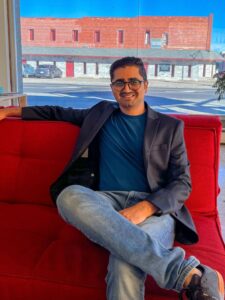
Exploring Data Democracy: Vinayak Mitty on AI, Machine Learning, and Empowering Businesses
By: Sunnie Dawn Baker A little over a year ago, I had the opportunity to sit down with Vinayak Mitty, the Director of Data Science for LegalShield. We discussed his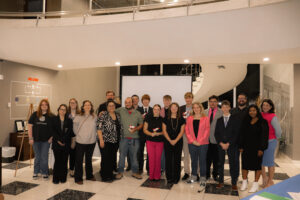
Conduit Startup Showcase: Celebrating Entrepreneurship and Community Innovation
By: Sunnie Dawn Baker Anticipation filled the air as fifteen entrepreneurs, representing nine different projects, prepared to present and compete for cash prizes. November 7th had finally arrived, and it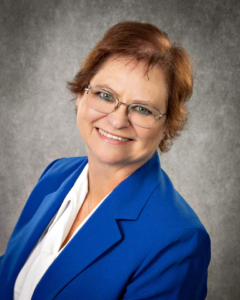